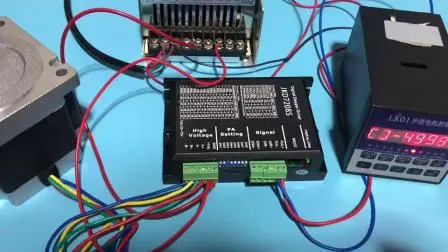
2 Phase 86mm Closed Loop Stepper Motor System
2 phase 86mm closed loop stepper motor system The Hybrid Servo Drive offers an alternative for applications requiring hi
Basic Info.
Model NO. | nema34 |
Condition | New |
Customized | Customized |
Material | Stainless Steel |
Input Voltage | 36 |
Pulse Input Frequency | 200 |
Volt | 20-50V |
Current | 8.0A Peak |
Transport Package | Expotr Carton |
Specification | CE/ROHS/HSG |
Trademark | JKONGMOTOR |
Origin | China |
Production Capacity | 100000PCS |
Product Description
2 phase 86mm closed loop stepper motor systemThe Hybrid Servo Drive offers an alternative for applications requiring high performance and high reliability when the servo was the only choice, while it remains cost-effective. The system includes a 3-phase stepper motor combined with a fully digital, high performance drive and an internal encoder which is used to close the position, velocity and current loops in real time, just like servo systems. It combines the best of servo and stepper motor technologies, and delivers unique capabilities and enhancements over both, while at a fraction of the cost of a servo system.
The Hybrid Servo Drive offers an alternative for applications requiring high performance and high reliability when the servo was the only choice, while it remains cost-effective.
NEMA 34 Hybrid Servo kit (closed-loop stepper system):one Hybrid Servo Driver HBS86 one NEMA34 JK86-4N-1000 Hybrid Servo Motor with one Encoder 1000 line, one 3 meter cable
A: HBS86, 3-phase Hybrid Servo Drive for NEMA34 Hybrid Servo Motor
Features
· Closed-loop, eliminates loss of synchronization
· Broader operating range - higher torque and higher speed
· Reduced motor heating and more efficient
· Smooth motion and super-low motor noise
· Do not need a high torque margin
· No Tuning and always stable
· Fast response, no delay and almost no settle time
· High torque at starting and low speed, high stiffness at standstill
· Lower cost
24-70V, 8.2A Peak, No Tuning, Nulls loss of Synchronization
Parameters | HBS86 | |||
Min | Typical | Max | Unit | |
Output current | 0 | - | 8.2 (Peak) | A |
Input voltage | 30 | 48 | 80 | VDC |
Logic signal current | 7 | 10 | 16 | mA |
Pulse input frequency | 0 | - | 200 | kHz |
Isolation resistance | 500 | MΩ |
Control Signal Connector - Screw Terminal | |||||||
Pin | Name | I/O | Description | ||||
1 | PUL+ | I | Pulse signal: In single pulse (pulse/direction) mode, this input represents pulse signal, each rising or falling edge active (software configurable, see hybrid servo software operational manual for more detail); In double pulse mode (software configurable), this input represents clockwise (CW) pulse, active both at high level and low level. 4-5V when PUL-HIGH, 0-0.5V when PUL-LOW. For reliable response, pulse width should be longer than 10μs. Series connect resistors for current-limiting when +12V or +24V used. The same as DIR and ENA signal. | ||||
2 | PUL- | I | |||||
3 | DIR+ | I | Direction Signal: In single-pulse mode, this signal has low/high voltage levels, representing two directions of motor rotation. In double-pulse mode (software configurable), this signal is counter-clock (CCW) pulse, active both at high level and low level. For reliable motion response, DIR signal should be ahead of PUL signal by 5μs at least. 4-5V when DIR-HIGH, 0-0.5V when DIR-LOW. Please note that rotation direction is also related to motor-driver wiring match. Exchanging the connection of two wires for a coil to the driver will reverse motion direction. The direction signal's polarity is software configurable. | ||||
4 | DIR- | I | |||||
5 | ENA+ | I | Enable signal: This signal is used for enabling/disabling the driver. In default, high level (NPN control signal) for enabling the driver and low level for disabling the driver. Usually left UNCONNECTED (ENABLED). Please note that PNP and Differential control signals are on the contrary, namely Low level for enabling. The active level of ENA signal is software configurable. | ||||
6 | ENA- | I | |||||
7 | ALM+ | O | Alarm Signal: OC output signal, active when one of the following protection is activated: over-voltage, over current, short circuit and position following error. This port can sink or source 20mA current at 24V. In default, the resistance between ALM+ and ALM- is low impedance in normal operation and become high when HBS57 goes into error. The active level of alarm signal is software configurable. See Hybrid servo software operational manual for more detail. | ||||
8 | ALM- | O | |||||
Encoder Feedback Connector - DSub15 Female | |||||||
Pin | Name | I/O | Description | ||||
1 | EA+ | I | Encoder channel A+ input | ||||
2 | EB+ | I | Encoder channel B+ input | ||||
3 | EGD | GND | Signal ground | ||||
4 | HW | I | Reserved | ||||
5 | HU | I | Reserved | ||||
6 | FG | GND | Ground terminal for shielded | ||||
7 | EZ+ | I | Reserved | ||||
8 | EZ- | I | Reserved | ||||
9 | HV | I | Reserved | ||||
10 | NC | - | Not Connected | ||||
11 | EA- | I | Encoder channel A- input | ||||
12 | EB- | I | Encoder channel B- input | ||||
13 | VCC | O | +5V @ 100 mA max. | ||||
14 | NC | - | Not Connected | ||||
15 | NC | - | Not Connected |
WHY YOU CHOOSE US:
We are a professional manufacturer for Stepper motor , Stepper driver, BLDC motor and DC motor. we can supply OEM service.
Our products all with CE and ROHS.
Welcome you visit our company Changzhou Jingkong Motor&Electric Appliance Co.,Ltd
Depending on advanced technology and knight service, we establish a good and diligent team and keep nice business relationship with a large amount of worthy clients in global market. We are prepared to provide the best products to clients at competitive price.
High quality .
Competitive price ,Good Packing , Fast Delivery .Knight service
Advanced technology
Believe that we will do our best!
Our Products:Our Packing:About our company:
24 :next
Send to us